Start at End: Choose Analytics Before Implementing Wireless Vibration Monitoring
Analytics are key to competing successfully in the
Industry 4.0 global environment. The Industrial Internet of Things (IIoT) promises to deliver accurate predictive analytics that minimizes expensive plant downtime by ensuring maintenance happens before assets fail. That’s a powerful, transformative result from a few hundred sensors linked by cellular connectivity. Too often, the end result falls far short of the promise. Are industry executives’ expectations too high, or is implementation missing the mark? Based on our experience of monitoring more than 4.3 million industrial assets, we think failure to deliver is all about analytics – actionable analytics.
All too often, companies with industrial assets spend more time deciding which wireless sensors they’ll use rather than strategically choosing the analytics they’ll monitor. Unfortunately, it’s not until the end of the five-phase implementation process that industrial executives discover they are receiving detailed analytics that are either not actionable, don’t matter or both. Teams find they are inundated with data and asset failure rates are the same or, worse yet, higher.
The most efficient and effective way to avoid this disappointing result is to focus on analytics first and implementation second when moving to a wireless vibration monitoring system like our
Wi-care™ product series.
All rotating assets have vibration that is captured in a raw signal resembling a waveform. The waveform, which resembles an EKG showing the electrical activity of a human heart, reports on a variety of potential issues related to machine health. However, not all measurements have value. Specific peaks in the waveform report the frequency and amplitude of each plotted component, associating peaks with imbalance, misalignment and looseness. Most often, pump, bearing and gear failures lead to unscheduled downtime. In 70% of these outages, lubricant failure is found to be the root cause of the downtime. The difficulty comes in that lubrication failures are more difficult to detect and can easily be overlooked by standard sensors. As sensors’ detection capabilities rise, so do their cost, which makes cost justification analyses invaluable as industrial executives weigh in on which analytics are reliable enough to be affordably monitored.
Vibration Monitoring Solution: Considerations for Choosing On-premise or the Cloud
Determining where you will host the wireless vibration monitoring solution, either on-premise or in the cloud, requires a deep understanding of your options and the impact of the options you choose. For example, industrial executives need to consider their choice from eight different perspectives, including security, compliance, compatibility, hardware, licensing, maintenance and management, uptime and analysis responsibility, to minimize installation surprises.
The following chart spells out the responsibilities associated with these two common approaches:
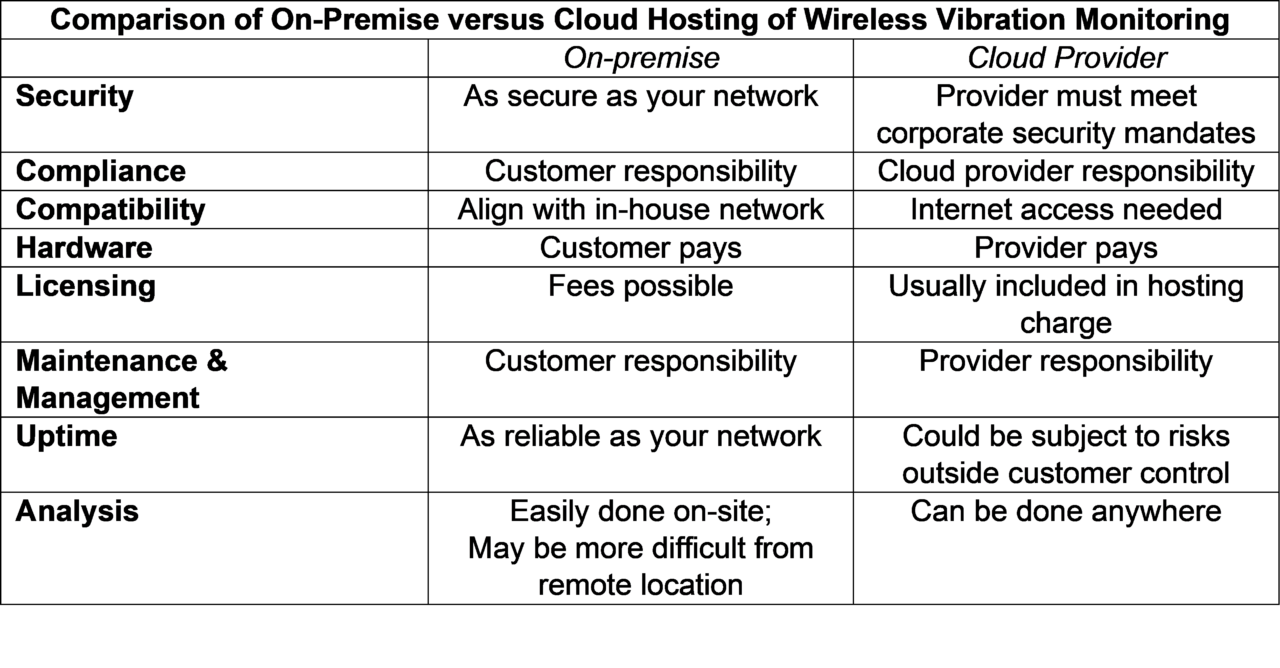
Choosing to host an on-premise vibration monitoring solution puts the majority of operational responsibility on your organization. While cloud providers take many of the hosting responsibilities on themselves, you’ll lose some of the control that is inherent in having the vibration monitoring solution on site.
In a future blog post, we will discuss implementation tips based on a five-stage launch cycle and how analytics and implementation go hand in hand.
If you have questions about which approach is more appropriate for your organization,
Contact us and request a call from one of our solution experts.