Harvesting Energy Savings from Industrial Assets
Many plant operations directors, maintenance managers and their teams view excessive energy use and downtime as unavoidable byproducts of industrial manufacturing – but they’re not.
Since 2004, we’ve monitored 67 billion assets and found that 99% of all failures can be predicted. Knowing which assets are most likely to stop operating, and when, allows manufacturers to reduce downtime by as much as 20% and
cut maintenance costs by at least 35%.
In this review of some of the most common locations of energy drain in manufacturing operations, we can help you identify targeted actions you can take – and quick wins you can achieve – to reduce wasted energy consumption, cut costs and make management stand up and take notice.
Identify leaks at network level
Most manufacturing operations lose a great deal of energy from their steam traps, a loss which compromises process efficiency. Pinpointing and resolving egregious leaks in just 10 to 20 traps across their network optimizes the entire trap system’s energy transport capabilities and improves steam quality.
Industrial manufacturing sites that use compressed gas networks – such as nitrogen, hydrogen and argon but mostly compressed air – find that leaks, even non-audible ones, can waste significant amounts of these expensive gases. It can be particularly difficult to spot leaks in pipes located high above the factory floor. In most industrial plants, at least one of every three compressors is working to compensate for leaks. In most instances, the continued use of energy even when the system is down leads to the leaks’ discovery. Leaking hydrogen is more than expensive; it’s dangerous. Because of hydrogen’s explosive volatility, acceptable levels of leakage are extremely low and set by industry regulators. Failing to adequately monitor and control hydrogen leakage can result in significant fines.
Visual inspection falls short when it comes to detecting gas leaks, which continue even when a piece of equipment is not operating. Using wireless, non-intrusive pipe monitoring technology solves both of those challenges. It takes only a few hours of wireless pipe monitor use to discover the one in three compressors that is leaking, on average, in a production facility. On average, improving the
efficiency of steam traps can save 10% to 25% of steam energy previously lost at each of the troublesome traps while correcting leaks in the compressed air system can produce air savings of 20% to 40%.
Check for friction, unbalanced components, lack of lubrication
Friction stemming from misaligned shafts not only reduces efficiency, but it also wastes energy. Proactively measuring and monitoring shaft alignments to diagnose and repair misalignments results in energy savings which, although minute, support Industry 4.0 initiatives.
In production facilities with complex industrial assets, that equipment can be re-aligned with non-intrusive technology to stop the friction and restore peak efficiency in less than half a day.
Being out of balance can plague turbines, fans and other rotating equipment, generating friction and vibrations. Potential savings of as much as 10% of each asset’s rotating energy are available to companies that keep these complex industrial assets in balance.
Innovative non-intrusive technology can resolve the balancing issues in a few hours, which extends each asset’s lifetime.
Much like the efficiency losses that come from out-of-balance assets, lacking the proper lubricant in the optimal amount and applied to the correct location, assets can run roughly, consume more energy than needed and undergo more strain – all factors that shorten optimal lifespan.
A
Total Reliability Centered Lubrication Program (TRCLP) monitors lubricant use, especially lubricant volume, wear and level of contamination, to reduce energy consumption. TRCLPs that include vibration maintenance for the life of named industrial assets help assure efficient operation and maximum lifespan.
Inconsistent temperatures compromise quality
Manufacturing plants, especially recipe- and formula-driven operations, frequently have gaps in their steam network insulation with some of these interruptions resulting in a total lack of insulation. These gaps not only affect process quality and energy consumption, but uninsulated sections of pipes also pose a physical danger to those working in the area who may touch them unintentionally.
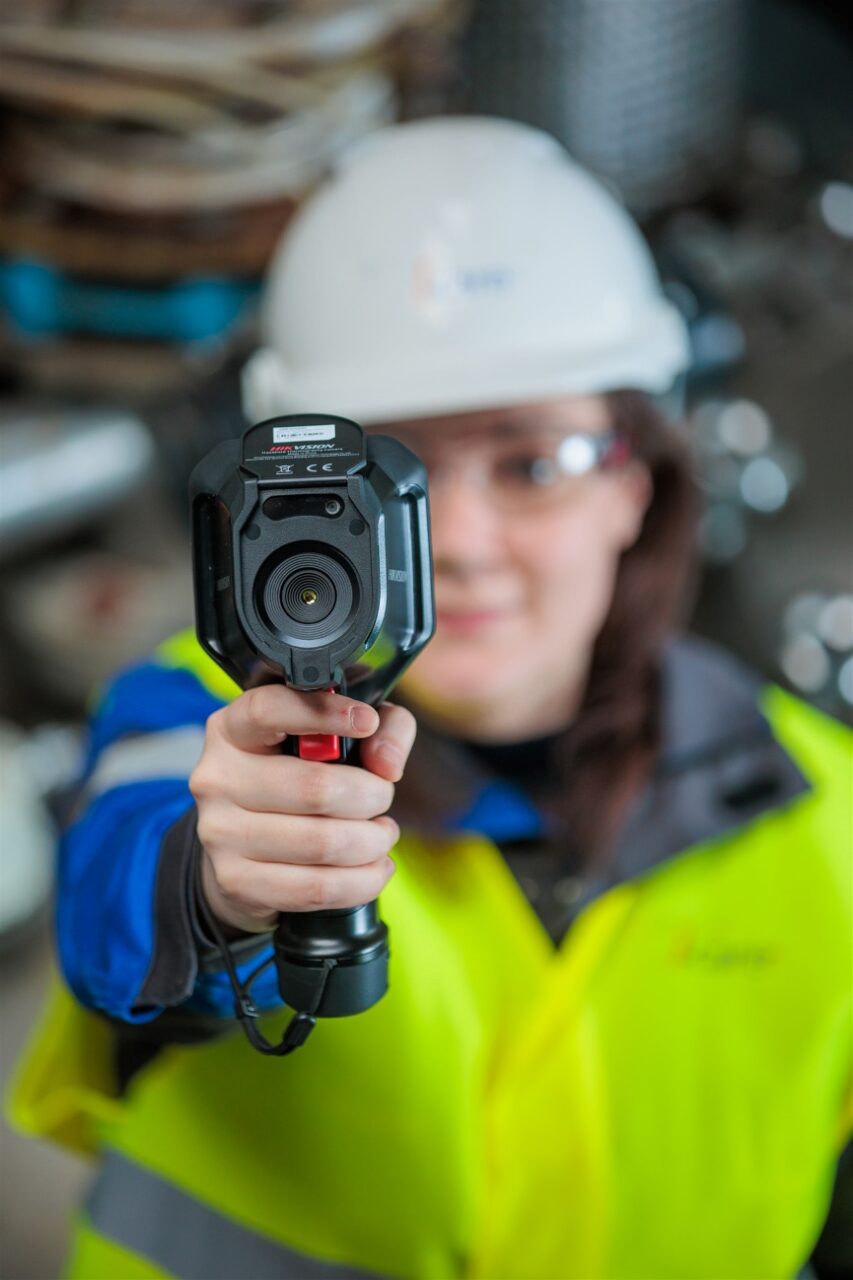
Infrared Inspection
Infrared thermography offers an exacting and fast way to create and maintain the finely calibrated readings required by manufacturing processes. In addition, this technology produces the exacting temperature readings critical to safeguarding human life.
Infrared thermography detects even the most minute insulation leak in a physical plant. Resolving temperature inconsistencies in electrical cabinets and components, for example, can save manufacturers as much as 25% of electrical energy costs. These documented savings can be leveraged to lower insurance expenses in some cases as well.
Infrared thermography not only identifies energy loss from the pipes lacking insulation, it also produces a surface temperature reading. Energy savings of up to 95% can be achieved by addressing inconsistent pipe insulation.
Specialized expertise to resolve energy loss, reap savings
Manufacturing operations offer a myriad of opportunities for energy loss as even small leaks can compromise product efficacy and quality. Additionally, the financial impact of ongoing, systemic energy losses can be substantial. Partnering with an energy expert that can accurately diagnose energy leakage, make needed adjustments and repairs quickly, and keep production flowing is critical to manufacturers’ being able to meet customers’ aggressive deadlines. These energy-saving approaches require a detailed look at the entire physical plant operation as well as a drill down inspection into areas where leaks and other energy-compromising issues are in play. While an energy audit takes only a few days to be completed and offers manufacturers close-to-immediate results, it takes specialized tools, an experienced eye and attention to detail to find not some, but all, of the issues.
At I-care, we work with leading industrial manufacturers to identify and resolve energy leaks, harvesting financial savings and restoring safe environments for employees. We support Industry 4.0 as it refocuses industrial manufacturing on achieving peak efficiency and optimal output. To learn how we can help your industrial manufacturing operation predict previously unpredictable asset failures, visit
www.icareweb.com/ or email Pierre Colon,
[email protected].