-
+850
Mitarbeiter in der ganzen Welt
-
36
Niederlassungen in 16 Ländern
-
+300k
Täglich überwachte Maschinen
-
67B
Überwachter Wiederbeschaffungswert (RAV)
Redefining Predictive Maintenance: Conquering Electric Motor Failures with Multimodal Mastery
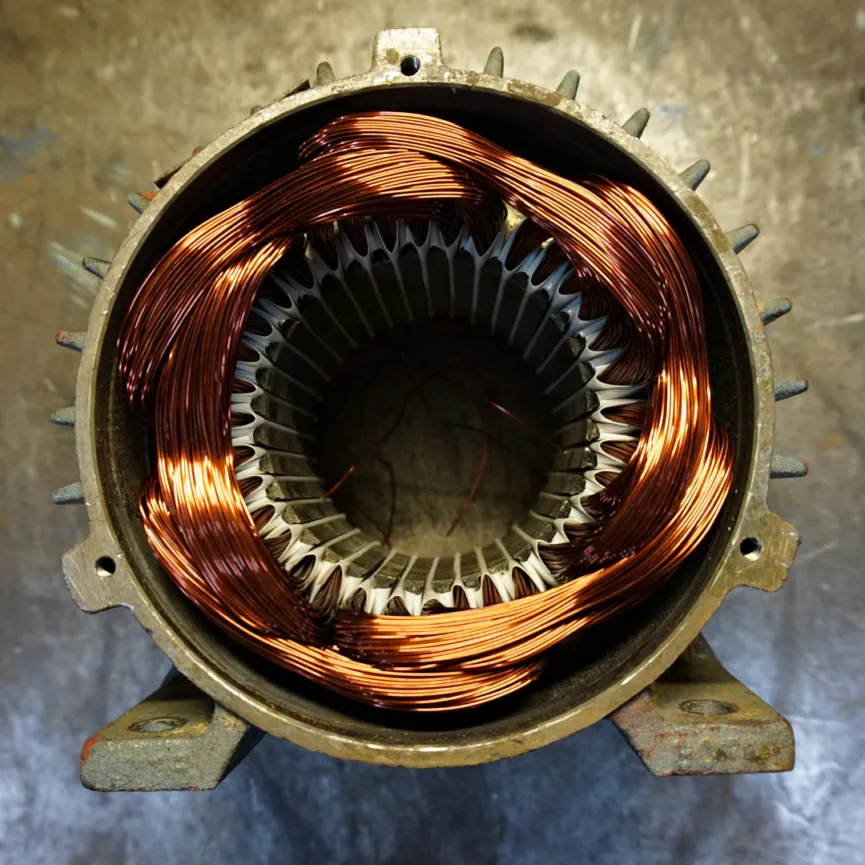
Properly timed maintenance of electric motors is essential for the reliability of production processes in almost every industry. As a result, the majority of maintenance managers prefer a predictive strategy to determine the timing of interventions for their critical motors. An effective predictive maintenance program indeed avoids unnecessary maintenance and limits the risk of secondary damage and unplanned downtime due to unexpected failures.
When selecting predictive maintenance technologies applicable to electric motors, numerous options come to mind. Vibration analysis, ultrasound (US), infrared thermography (IRT), electrical signature analysis (ESA), motor circuit analysis (MCA), lubricant analysis, and visual inspection can all provide valuable information about the motor’s condition. The combination of several (or all) of these techniques provides the most complete picture of the motor’s health, though it may be justified only for the most critical installations. The question then arises: which one(s) to choose?
This paper focuses on vibration analysis and motor testing, as these are often subjects of debate when determining efficient and versatile predictive technologies for electrical motors. In discussing motor testing, it’s important to distinguish between online motor testing performed when the motor is energized and offline testing on a de-energized motor.
Figure 1. Motor current signature analysis using FFT. |
Offline motor testing, often referred to as motor circuit analysis (MCA) or motor circuit evaluation (MCE), predominantly detects failure modes related to stator winding, insulation, cabling, and connections. Air gap and squirrel cage condition can also be evaluated. Most of these failure modes (e.g., insulation faults, cable degradation, faulty contacts, loose connections, developing winding faults, ground faults) cannot be detected using other technologies. While MCA requires the motor to be electrically disconnected prior to testing, it can be time-consuming. For this reason, it is often used as an inspection method for incoming and outgoing motors or troubleshooting, and it also fits well in a periodic inspection program. In low voltage applications, with proper preparation, inspections can be efficiently performed, allowing up to 25 motors to be tested in an 8-hour day. On high-voltage motors, testing will require considerably more time as partial discharge and tan delta measurements need to be added, but they are usually critical installations in a plant.
Motor current signature analysis (MCSA) and electrical signature analysis (ESA) assess the health of the motor system while operating. While MCSA theoretically only measures motor current and ESA measures both current and voltage, often both terms are used interchangeably. Hence, MCSA is often used to refer to online motor analysis, including voltage measurements as well. Online motor analysis provides an excellent means to determine both stator and rotor health and monitor motor efficiency. It also detects issues in power supply and controls. Online motor testing is particularly suitable for permanent monitoring combined with automated problem detection, without the need for expensive additional monitoring systems.
Vibration analysis, whether applied periodically or online, is the most powerful technique for detecting a wide range of mechanical issues in motors (and rotating equipment in general). Bearing defects, misalignment, looseness, imbalance, resonance, and lubrication issues all affect vibration behavior.
Figure 2. Vibration analysis using wireless sensors. |
Some electrical problems, such as rotor-related defects or soft foot, can also be detected with vibration measurements, but the electrical signature analysis will be more accurate in determining those.
Conversely, certain mechanical defects will be detectable with motor current signature, but vibration will be the most accurate. The most sensitive technique is one that directly measures the primary physical effect generated by the defect. This leads to the table in Figure 3, summarizing the applicability of different predictive technologies for different failure modes.
Figure 3. Applicability of different predictive technologies. |
Determining which measurement technique to prefer as the first technology also depends, of course, on which defects are most likely to occur. Although it is difficult to determine the precise proportion of different root causes of motor failure in the industry today, a frequently cited study conducted by EASA (Electrical Apparatus Service Association) is shown in Figure 4. According to this study, conducted in the early 2000s, more than half of motor failures can be attributed to bearing issues.
Depending on a plant’s specific situation, the actual numbers may differ, but the fact remains that bearing defects are responsible for a significant part of motor failures. In addition, vibration analysis will ensure that the incidence of bearing damage can be greatly reduced by timely detection of root cause problems such as imbalance, alignment issues, resonance, and, certainly, lubrication problems. These are much more difficult (or, in the case of lubrication problems, virtually impossible) to detect with electrical measurements.
Figure 4. Causes of electrical motor failure |
In summary, it is true that each of the three technologies – vibration analysis, online, and offline motor analysis – has specific advantages and allows the detection of failure modes that are impossible or difficult to achieve with other techniques. For a given situation, the probability of each failure mode times the detection sensitivity, balanced against the cost of implementation, can be a good indicator to choose a strategy. Vibration analysis is often chosen as the first predictive technique due to its cost-effective nature in many situations, enabling reliable monitoring of both motor and driven machine for a range of failure modes responsible for the majority of machinery problems. In other situations, however, the application of vibration analysis can be complicated by problematic accessibility, and the choice of online electrical measurements will be more obvious.
If you have questions or want to speak to one of subject matter experts, contact us today!